With a large variety of applications, there is not one single configuration or size of blast equipment to meet all production requirements. Gibson Abrasive Equipment offers a wide range of batch and continuous production style machines. In this feature, we are going to put an emphasis on the equipment utilized in the batch-style production process and review some of Gibson’s offerings in that category.
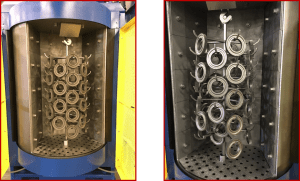
Gibson spinner hanger blasting systems provide a cost-effective solution to batch cleaning. They are designed and built for ease of use and efficiency. Spinner hanger systems are typically used for higher production requirements of where part-on-part contact from tumbling is not acceptable.
Multi-station spinner hangers are unique because they have at least two chambers and do not require a door to be opened/closed for the blasting process to take place. The blasting process is going in conjunction with the operator or robot unloading clean parts and reloading a new batch.
Applications:
- Allows for multiple parts that you can hang on a tree.
- While one chamber is blasting, the other chamber is unloading and loaded again for the next cycle.
Advantages:
- The operator never sits idle always loading or unloading the system.
- The cycle will sometimes be faster than the operator can perform the unloading and loading process.
Applications:
- Allows for multiple parts that can hang on a tree.
- Used to hang heavy parts when a dual chamber unit doesn’t make sense.
Advantages:
- Larger or awkward parts have more movement for swing.
- Easier to hit different angles due to oscillation & part moving ability.
- Can be used with monorails.
- Easier to load with a crane.
- Better accessibility to fixtures/trees.
Gibson Table Blasters are ideal for blasting large heavier pieces that are typically difficult to hang, and should not be tumbled together. A table blast machine consists of a single table that rotates in the blast zone.
Table Blasting: Before & After
Gibson’s widely popular XT series of tables has multiple oscillating blast wheels that allow for additional blast coverage angles, hitting the otherwise hard to reach pockets on parts.
Table blast machines are available in table diameter sizes ranging from 3’ up to as large as 10’ and capable of extremely heavy weight capacities.
Applications:
- Large parts that are difficult to hang or tumble.
- Companies that are going to run a variety of parts.
Advantages:
- Multipurpose – Parts can be placed on the table or hung on a fixture. (mounted on the table)
- Allows for larger parts and smaller parts in the same machine.
Gibson Tumble Blast systems utilize a continuous rubber belt with tumbling ridges that gently tumble the batch of parts to mix and expose them to the blast for consistent blast coverage of the entire batch.
Tumble Blasting: Before & After
The tumble blast systems can be operated manually, semi-automated, or even fully automated due to the integration of loading/unloading hoists and conveyors.
Applications:
- Batches of parts that can tumble on top of each other without causing damage to the parts.
Advantages:
- Can run large batches of smaller parts all together.
- No manual flipping or rotating.
- Blasting on all sides if parts tumble properly.
The optimal shot-blast equipment solution starts with a discussion about your surface preparation requirements and a proposed processing method. As an original equipment manufacturer, Gibson forges strong relationships with many premier companies. We offer short lead-times, unbiased processing recommendations, and experienced staff to assist in every phase from design to installation.
Contact us to discuss your next blast application:
888-867-1619